Кислородный конвертер: устройство и технология выплавки стали
Содержание:
- I ВВЕДЕНИЕ
- Определение «Кислородно-Конвертерный Процесс» по БСЭ:
- Торкретирование футеровки
- Футеровка кислородного конвертера
- Механизм поворота
- Томасовский способ
- Футеровка кислородных конвертеров
- б) металлический лом
- Кислородно-конвертерный процесс
- Кислородно-конвертерный способ производства стали
- Плавка в конвертере с донной продувкой протекает следующим образом.
- а) расплавленный чугун
- Заключение
I ВВЕДЕНИЕ
60% сырой стали приходится от общего объема мирового производства, кислородно-конвертерный способ производства стали, является доминирующей технологией металлургического производства. В США этот показатель составляет 54% и постепенно снижается, связано это прежде всего с появлением на листопрокатных заводах электродуговой печи (ЭДП) «Гринфилд». Тем не менее, в других странах его использования возрастает.
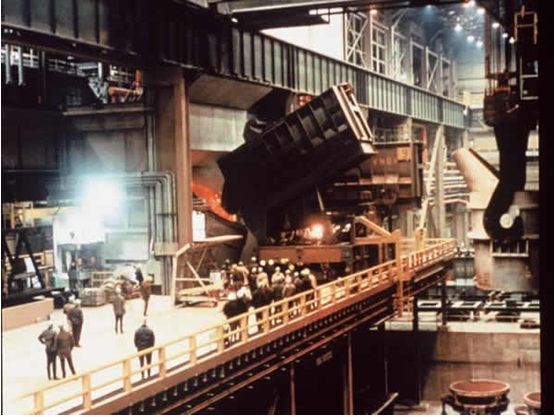
Рисунок 1 – Загрузка металлического лома в кислородный конвертер на сталеплавильном заводе. Справа показан ковш с жидким чугуном.
Существует несколько способов подачи кислорода в конвертер: продувка ванны кислородом сверху, донное дутье и комбинация этих двух способов. Рассмотрим только способ продувки ванны, жидкого металла, кислородом сверху.
Кислородно-конвертерный способ выплавки стали отличается от электросталеплавильного меньшими затратами на энергию. Основным сырьем кислородного-конвертера являются 70-80% жидкого чугуна из доменных печей и стального лома. Которое загружают в конвертер. После производится продувка конвертера чистым кислородом (> 99,5%) под высоким давлением. Кислород окисляет углерод и кремний, содержащиеся в расплавленном металле с выделением большого количества тепла, которое расплавляет металлический лом. Это приводит к меньшим энергетическим затратам при окисления железа, марганца и фосфора. Выделенное тепло передается обратно в ванну при выходе из конвертера угарного газа.
Продукт кислородно- конверторной выплавки стали, является расплавленная сталь с заданными химическим свойствами при температуре 2900 ° F-3000 ° F. Далее сталь может подвергаться вторичной переработке или быть направлена непосредственно на машину непрерывного литья заготовок (МНЛЗ), где она затвердевает в форме: блюма, заготовки, или плиты.
Основой является оксид магния (MgO), который при контакте с расплавом образует основные шлаки. Эти шлаки, необходимы для удаления фосфора и серы из расплава.
Около 250 тонн, за один раз, составляют размеры выплавки стали в США, около 40 минут, из которых 50% -«продувка». Этот показатель производства составил совместимость процесса с непрерывной разливки слябов, которые, в свою очередь, оказали огромное положительное воздействие на доходы, от продажи сырой стали до готовой продукции, с переработкой плоского качества проката.
Определение «Кислородно-Конвертерный Процесс» по БСЭ:
Кислородно-конвертерный процесс — один из видов передела жидкого чугуна в сталь без затраты топлива путём продувки чугуна в Конвертере технически чистым кислородом сверху. О целесообразности использования кислорода при производстве стали в конвертерах указывал ещё в 1876 русский металлург Д. К. Чернов. Впервые применил чистый кислород для продувки жидкого чугуна снизу советский инженер Н. И. Мозговой в 1936. В 1939-41 на Московском заводе станкоконструкций проводились опыты по продувке чугуна сверху кислородом в 1,5-т ковше и выплавлялась сталь для фасонного литья. Впервые К.-к. п. был опробован в промышленном масштабе в Австрии в 1952. Первый кислородно-конвертерный цех в СССР был введён в эксплуатацию в Днепропетровске на металлургическом заводе им. Петровского в 1956.К.-к. п. осуществляется в конвертере с основной смолодоломитовой (доломит, смешанный со смолой) футеровкой и с глухим дном. кислород под давлением более 1 Мн/мІ (10 кгс/смІ) подаётся водо-охлаждаемой фурмой через горловину конвертера. С целью образования основного шлака, связывающего фосфор, в конвертер в начале продувки добавляют известь. Под воздействием дутья примеси чугуна (кремний, марганец, углерод и др.) окисляются, выделяя значительное количество тепла, в результате чего одновременно снижается примесей в металле и повышается температура, поддерживая его в жидком состоянии. Когда содержание углерода достигает требуемого значения (количество углерода определяется по времени от начала продувки и по количеству израсходованного кислорода), продувку прекращают и фурму извлекают из конвертера. Продувка обычно длится 15-22 мин. Полученный металл содержит в растворе избыток кислорода, поэтому заключительная стадия плавки — раскисление металла. Течение К.-к. п. (т. е. последовательность реакций окисления примесей чугуна) обусловливается температурным режимом процесса и регулируется изменением количества дутья или введением в конвертер«охладителей» (Скрапа, железной руды, известняка). Температура металла при выпуске около 1600°C. На приведена схема получения стали в кислородном конвертере.Применение при конвертировании кислородного дутья вместо воздушного (см. Бессемеровский процесс, Томасовский процесс) позволило получать сталь с низким содержанием азота (0,002-0,006%). Высокая температура К.-к. п. способствует интенсивному окислению углерода, поэтому содержание кислорода, растворенного в металле, снижается до 0,005-0,01%. Расход кислорода на 1 т чугуна при К.-к. п. составляет&asymp. 53 мі. При одном и том же качестве стали К.-к. п. по сравнению с мартеновским (см. Мартеновское производство) даёт экономию по капиталовложениям на 20-25%, снижение себестоимости стали на 2-4% и увеличение производительности труда на 25-30%. В СССР за 1965-71 выплавка стали в кислородных конвертерах увеличена с 4 до 23,2 млн.т в год, или в 5,8 раза. Рост производства конвертерной стали сопровождается ростом ёмкости конвертеров. С технологической точки зрения, увеличение емкости конвертера не создает каких-либо дополнительных трудностей ведения плавки. Поэтому даже в крупных конвертерах выплавляют не только рядовую низкоуглеродистую сталь, но и среднеуглеродистую, высокоуглеродистую, низколегированную и легированную стали.Лит.: Применение кислорода в конвертерном производстве стали, М., 1959. Туркенич Д. И., Автоматизация процесса плавки в кислородном конвертере, , 1966: Бережинский А. И., Хомутинников П. С., Утилизация, охлаждение и очистка конвертерных газов, М., 1967. Явойский В. И., Теория процессов производства стали, 2 изд., М.. 1967. Конвертерные процессы производства стали, М., 1970.С. Г. Афанасьев.Схема получения стали в кислородном конвертере: а — загрузка металлолома. б — заливка чугуна. в — продувка. г — выпуск стали. д — слив шлака.
Торкретирование футеровки
Под агрессивными температурно-химическими воздействиями внутренние поверхности конструкции конвертера быстро утрачивают свои качества – опять же, это касается внешнего износа рабочего слоя термической защиты. В качестве ремонтной операции применяется торкретирование футеровки. Это технология горячего восстановления, при которой с помощью специального оборудования укладывается огнеупорный состав. Его наносят не сплошным способом, а точечно на сильно изношенные участки базовой футеровки. Процедура выполняется на специальных торкрет-машинах, подающих к поврежденному участку водоохлаждаемую фурму с массой из коксовой пыли и магнезитового порошка.
Футеровка кислородного конвертера
Обязательная технологическая процедура, в ходе которой внутренние стены конвертера обеспечиваются защитным слоем. При этом надо учитывать, что в отличие от большинства металлургических печей данная конструкция подвергается гораздо более высоким термическим нагрузкам, что обуславливает и особенности выполнения футеровка. Это процедура, предполагающая укладку двух защитных слоев – функционального и армирующего. Непосредственно к поверхности корпуса примыкает пласт защитной арматуры толщиной 100-250 мм. Его задача заключается в снижении теплопотерь и недопущении прогара верхнего слоя. В качестве материала применяется магнезитовый или магнезитохромитовый кирпич, который может служить годами без обновления.
Верхний рабочий слой имеет толщину порядка 500-700 мм и заменяется довольно часто по мере износа. На этом этапе кислородный конвертер обрабатывается безобжиговыми песко- или смоловязанными огнеупорными составами. Основу материала для этого слоя футеровки составляет доломит с добавками магнезита. Стандартный расчет по нагрузке делается исходя из температурного воздействия порядка 100-500 °С.
Механизм поворота
Механизм поворота обеспечивает вращение конвертера вокруг оси цапф на 360° со скоростью (частотой) от 0,1 до 1мин-1 . Механизм поворота может быть односторонним и двухсторонним. У конвертеров вместимостью 130т и менее делают односторонний механизм поворота, в котором одна из цапф соединена с приводом (см. рис. 2). У большегрузных конвертеров опорное кольцо при повороте подвергается большим усилиям. Поэтому для более равномерного их распределения механизм поворота большегрузных конвертеров делают двухсторонним (см.рис. 3). Этот механизм имеет два синхронно работающих привода, каждый из которых соединен с одной цапфой.
Механизмы поворота бывают стационарными и навесными. Первые конвертеры имели стационарный механизм поворота, жестко закрепленный на отдельной опоре. Такой механизм имеет (см. рис. 2) два электродвигателя 6 (один из них резервный), связанный с ними двухсторонний червячный редуктор 5 и тихоходный редуктор 4, соединенный с цапфой конвертера через зубчатую муфту 3. Недостатком механизма является его быстрый износ вследствие того, что будучи неподвижно закрепленным он испытывает удары вращающихся цапф в случае их перекоса, а также ударные нагрузки в момент включения привода.
Современные конвертеры имеют более совершенный навесной (закрепленный на цапфе) привод (см. рис. 3). На цапфе жестко закреплено ведомое зубчатое колесо 4, закрытое корпусом 7; этот корпус опирается на цапфу через подшипники и от проворачивания его удерживает демпфер 9. Таким образом при вращении зубчатого колеса 4 с цапфой, корпус 7 остается неподвижным. Зубчатое колесо вращают несколько (от 4 до 6) электродвигателей с редукторами 6, выходные валы-шестерни 5 которых входят в зацепление с колесом; эти валы-шестерни через подшипники крепятся в отверстиях стенки корпуса 7. Электродвигатели с редукторами держатся (навешены) на валах-шестернях 5; вращая валы, сами двигатели остаются неподвижными, так как удерживаются от проворачивания демпферами 8.
Рисунок 10. — Кинематическая схема навесного многодвигательного привода конвертера
На рисунке 10 показана кинематическая схема аналогичного навесного двухстороннего привода. В ней выделяют электродвигатели 5 (их четыре) с тормозами, быстроходные трехступенчатые редукторы 4-, тихоходные редукторы 1 (зубчатое колесо 7, вал-шестерня 6). В каждом из четырех приводов электродвигатель через быстроходный редуктор вращает вал-шестерню и, тем самым, зубчатое колесо и цапфу 2 с опорным кольцом 9. Цапфы установлены в подшипниковых опорах; опора 10— фиксированная, опора 8 — плавающая.
Навесной многодвигательный привод по сравнению со стационарным обладает следующими преимуществами: перекос цапф не влияет на его работоспособность, так как, будучи закрепленным на цапфе, привод перемещается вместе с ней; при выходе из строя одного двигателя привод остается работоспособным; демпферы частично компенсируют динамические нагрузки при включениях и торможениях, что снижает износ шестерен привода; в 2-3 раза уменьшается масса привода; существенно уменьшается площадь, необходимая для его установки.
Томасовский способ
Томасовский способ – продувка через жидкий металл воздуха, но футеровка основная и благодаря этому становится возможным удаление фосфора. Футеровка доломитовая (МgO, СаО). Применяется для переплавки в стали чугунов марок Т-1 и Т-2, содержащих повышенный % фосфора до 2,2% и серы.
В томасовском конвертере процессы окисления протекают в такой же последовательности, как и в бессемеровском, за исключением того, что в третьем периоде идет бурное окисление фосфора, за счет чего резко повышается температура стали и сталь становится более качественной и пластичной.
Для удаления Р и S в конвертер загружается 12-14% от веса заливаемого чугуна – известняк СаСО3:
Р2О5(СаО)4 – очень прочное соединение и ценное удобрение для сельского хозяйства.
– FeS + СаО → СаS + FeО, где СаS – непрочное соединение, поэтому вводят Mn:
СаS + MnO → MnS + СаО, где MnS – не переходит в ванну, если остается, то это более тугоплавкое соединение нежели FeS + Fe (tплавл. ≈ 988°С).
В настоящее время томасовский способ в нашей стране почти не применяется, так как высокофосфористых и высокосернистых руд у нас мало.
Рассмотренные конвертерные способы выплавки стали имеют следующие преимущества:
- Высокая производительность (время плавки 20-30 мин.).
- Простота конструкций печей (конвертеров) и следовательно малые капитальные затраты.
- Малые эксплуатационные затраты.
- Не требуется при плавке специально вводить тепло, так как оно получается в конвертерах за счет реакций окисления примесей.
- Значительный угар железа (до 13%).
- Невозможность переплавлять в больших количествах скрап (металлический лом).
- Более низкое качество стали (главный недостаток конвертирования) – например, за счет продувки воздухом в стали увеличивается содержание азота (до 0,025-0,048%), которое заметно снижает качество стали.
- Из-за непродолжительности процесса невозможно в конвертерах выплавлять стали сложного химического состава, а из-за невысоких температур (наибольшая tплавл. = 1600°С) невозможно добавлять тугоплавкие легирующие компоненты (W, Mo, Nb и т.д.).
Таким образом до настоящего времени конвертерное производство стали было ограничено из-за вышеизложенных недостатков. В конвертерах выплавлялись лишь простые углеродистые стали обыкновенного качества.
Футеровка кислородных конвертеров
Футеровка кислородных конвертеров состоит из двух слоев — арматурного, примыкающего к корпусу и рабочего. Арматурный слой толщиной 110-250мм выполняют из магнезитохромитового кирпича, он не требует замены длительное время (годы). Рабочий слой толщиной 500-800м, контактирующий с металлом и шлаком, преимущественно выкладывают из безобжиговых больше мерных кирпичей на основе доломита (35-50% MgO, 45-60% CaO) и реже магнезита (> 85 % MgO) со смоляной или пековой связкой. Измельченные огнеупоры смешивают при температуре 80-140°С с 5-7% каменноугольных смолы или пека и прессуют в кирпичи. Далее выкладывают футеровку рабочего слоя и обжигают ее, нагревая до 1100°С. При этом смола (пек) коксуется, т. е. удаляются летучие и остается тонкая коксовая (углеродистая) пленка, которая скрепляет зерна огнеупора и защищает их от взаимодействия со шлаком. На небольших конвертерах кладку делают из кирпичей в один ряд (рис. 5, а), на большегрузных — в два ряда вперевязку (рис 5,б). Стойкость такой футеровки составляет 500-700 плавок.
В последние годы стали широко применять магнезито-углеродистые (MgC с добавкой 10-20% С) кирпичи в сочетании с периодическим ошлакованием футеровки. Последняя заключается в том, что через 3-5 плавок шлак загущают и затем раздувают его (газом, подаваемым через фурму), в результате чего на футеровку налипает тонкий слой шлака, который на последующих плавках постепенно растворяется, а сама футеровка рабочего слоя почти не разрушается. При этом стойкость футеровка доведена до 3000-5000 плавок и более.
Поскольку теплопроводность магнезито-углеродистых огнеупоров значительно выше теплопроводности обычно применявшихся огнеупоров на смоляной связке, переход на магнезито-углеродистую футеровку приводит к заметному перегреву корпуса конвертера. Поэтому конвертер оборудуют системой труб и форсунок, охлаждающих корпус путем подачи водяного тумана (рассыпленной воды).
Футеровка летки имеет арматурный слой из магнезито-хромитового кирпича,затем слой огнеупорной массы на основе MgО и в середине блоки из плавленого магнезита, имеющие сквозные отверстия, образующие канал летки. Эти блоки заменяют через 60-120 плавок.
б) металлический лом
В кислородно-конвертерном процессе, лом на сегодняшний день является теплоотводом. В 20 — 25% это один из самых важных и дорогостоящих компонентов шихты.
Стальной лом доступен во многих формах. Основными категориями являются «метало-приеники», сформированные внутри завода. С появлением непрерывного литья, количество отходов уменьшилось и это вызвало необходимость, для комбинатов, покупки лома на рынке. Плоский прокат лома, как правило, хорошего качества не влияние на химию кислородно-конвертерного процесса. Существует потеря прибыли примерно на 2% за счет цинкового покрытия на оцинкованном ломе. «Запрос лома» образуется при производстве нержавеющей продукции. Очень быстро это находит свой путь в системе переработки. Многие сталелитейные заводы имеют соглашения с производителями, чтобы купить у них металлолом. «Устаревший» или «после потребителя» лом возвращается на рынок после того, как у продукта закончился срок службы. Банки возвращаются на рынок очень быстро, но автомобили имеют среднюю продолжительность жизни до 12 лет.
Лом также поставляется в различных размерах, изменяя различный химический анализ и различные цены. Все это делает покупку и переплавку лома очень сложным вопросом. Очень большие куски металлолома могут трудно плавятся и при загрузке могут повредить конвертер. Некоторые отходы могут содержать нефть или окисленные поверхности. Устаревший лом может содержать целый ряд других объектов, которые могут быть опасными или взрывчатыми веществами. Очевидно, что химический анализ лома является неточным
Выбор лома осложняется еще и широким спектром стальной продукции. Глубоко тянущая сталь ограничивает максимальное остаточное (% Cu +% Sn +% Ni +% Cr +% Mo) содержимое менее чем 0.13%. В то время как другие продукты позволяют этому диапазону быть выше 0,80%. Поскольку эти элементы не могут быть окислены из стали, их содержание в конечном продукте может быть уменьшено путем разбавления с очень высокой чистоты ломом или расплавленного металла. Использование низкой остаточности жидкого чугуна в конвертере, с присущей ей эффективностью разбавления, является одной из особенностей, отличающих кислородно-конверторный процесс от электросталеплавильного.
Кислородно-конвертерный процесс
Устройство кислородного конвертера. |
Кислородно-конвертерный процесс — это выплавка стали из жидкого чугуна в конвертере с основной футеровкой и продувкой кислородом через водоох-лаждаемую фурму.
Последовательность технологических операций при выплавке стали в кислородных конвертерах. |
Кислородно-конвертерный процесс заключается в продувке жидкого чугуна кислородом. Кислородный конвертер — это сосуд грушевидной формы из стального листа, выложенный изнутри основным огнеупорным кирпичом. Конвертер может поворачиваться на цапфах вокруг горизонтальной оси для завалки скрапа ( лома), заливки чугуна и слива стали и шлака.
Кислородно-конвертерный процесс позволяет получать стали с минимальными содержаниями газов — азота, кислорода, водорода.
Кислородно-конвертерный процесс представляет собой один из видов передела жидкого чугуна в сталь без затраты топлива путем продувки чугуна в конвертере технически чистым кислородом.
Изменение содержания СОг в отходящих газах по ходу кислородно-конвертерной плавки. |
Высокопроизводительный кислородно-конвертерный процесс является одним из наиболее важных металлургических объектов автоматизации. Усовершенствование его управления необходимо для получения стали с заданными температурой и составом при максимальной экономичности плавки. Однако задача полной автоматизации на основе совершенной модели процесса является крайне сложной и требует знания закономерностей воздействия множества факторов: физико-химических, газо-гидродинамических и других, до настоящего времени недостаточно исследованных. Поэтому автоматическое управление вводится этапами и ограничивается пока главным образом применением статического метода.
Кислородно-конвертерный процесс произ-ва стали отличается тем, что примеси чугуна окисляются технически чистым кислородом, к-рый подается через водо-охлажденные фурмы в глуходонный конвертер сверху под большим давлением. Основная футеровка конвертера позволяет образовывать шлак, способствующий удалению фосфора и серы из металла. Интенсивный нагрев металла в конвертере при кислородном процессе позволяет использовать для плавки не только руду, но и лом в количестве до 300 кг на 1 m стали.
При кислородно-конвертерном процессе передел чугуна с содержанием фосфора до 0 3 % не представляет технологических трудностей. При более высоком содержании фосфора в чугуне применяют специальные технологические приемы для удаления фосфора из металла. Для наиболее полной дефосфорации металла при кислородно-конвертерном процессе необходимо создать условия для образования активного известково-железисто-го шлака. Скорость дефосфорации металла зависит от химического состава шлака, его жидкотекучести, теплового режима и ряда других факторов.
Во-первых, кислородно-конвертерный процесс, предназначенный в основном для непосредственного превращения жидкого чугуна в сталь, не содержит такие трудноуправляемые чисто теплотехнические периоды, как завалка с прогревом и, в известной степени, расплавление твердой шихты. С самого начала конвертерной плавки ведется продувка фактически жидкой ванны, что сопровождается бурным обезуглероживанием и процессами окисления других элементов чугуна. При этом операторы воздействуют на ход плавки такими мощными средствами, как изменение расхода кислорода и положения кислородной фурмы.
Используя преимущества кислородно-конвертерного процесса ( бурное кипение, исключительно быстрое регулирование температуры), можно его применять для получения легированных сталей без значительного пони -, жения производительности. Основной трудностью при этом является введение легкоокисляющихся элементов во время продувки. К таким элементам относятся хром, кремний, марганец.
Шихтовыми материалами кислородно-конвертерного процесса являются жидкий передельный чугун, ( см. табл. 2.1), стальной лом ( не более 30 %), известь для наведения шлака, железная руда, а также боксит ( А1203), плавиковый шпат ( CaF2), которые применяют для разжижения шлака.
Важнейшей особенностью кислородно-конвертерного процесса является быстрое окисление фосфора с начала подачи кислорода и особенно во второй четверти продувки.
Производство стали кислородно-конвертерным процессом характеризуется меньшими удельными капитальными затратами по переделу, высокой производительностью агрегатов и более высокой производительностью труда по сравнению с мартеновским производством.
Кислородно-конвертерный способ производства стали
В настоящее время промышленная индустрия настолько окрепла, что стало возможным в больших промышленных количествах получать промышленно чистый кислород. Продувая чугун кислородом имеется возможность выплавлять в них стали по качеству близкие к мартеновским. Кроме того благодаря применению О2 в конвертерах производительность их еще более повышается и также повышается температура ванны (tплавл. повышается до
2500°С), что позволяет уже в большем количестве в конвертерах переплавлять скрап. Кислородно-конвертерное производство позволило в последние годы выплавлять в конвертерах до 40% от общего количества выплавляемой стали.
Рисунок 1.2 – Кислородно-конверторный способ:
1 – горловина для загрузки, 2 – цилиндрическая часть, 3 – стальное кольцо с цапфами, 4 – съемное днище
При этом способе кислород подается в ванну жидкого чугуна в конвертере сверху, через охлаждаемую водой фурму.
Конвертерные установки с донной кислородно-топливной продувкой – в 1,5 раза превосходят по производительности 2-х ванную мартеновскую печь (при сохранении баланса металлолома).
Плавка в конвертере с донной продувкой протекает следующим образом.
В наклоненный конвертер загружают стальной лом и заливают жидкий чугун. При заливке конвертер поворачивают в почти горизонтальное положение, чтобы жидкий чугун не заливал фурм. Для защиты фурм от попадания чугуна и шлака через них продувают азот или воздух. Затем подают дутьё и конвертер поворачивают в рабочее вертикальное положение. В начале продувки вдувают порошкообразную известь иногда с добавкой плавикового шпата.
В ходе продувки окисляется избыточный углерод, кремний, марганец. Формируется шлак, в который удаляются фосфор и сера. За счет реакций окис-ления расплавляется металлолом и нагревается металл.Продувку заканчивают при заданном содержании углерода в металле.
Особенностью технологии процесса при донной продувке является то, что скорость обезуглероживания металла оказывается выше вследствие более инте-нсивного перемешивания ванны и увеличения поверхности раздела газ-металл, а также более полного усвоения кислорода. Технологические преимущества конвертерного процесса с подачей кисло-рода снизу послужили основанием для разработки вариантов технологии ком-бинированной продувки металла сверху и снизу.
а) расплавленный чугун
Горячий металл жидкого чугуна из доменных печей насыщен до 4,3% углерода, и 1% или менее кремния Si. Они транспортируются в конвертерный корпус от миксерами или ковшами. Химия расплава зависит от того, как доменная печь работает и как железосодержащие материалы отражаются в ней. Сегодня тенденция работать на высокой производительности с низкими объемами шлака и топлива, что приводит к снижению кремния и увеличению уровня содержания серы в чугуне. Если конвертерный шлак повторны используется, то уровни P и Mn резко возрастают, так как они проявляются почти в 100% горячего металла. В Американских железных рудах низкое содержание обоих элементов.
Содержание серы в доменной печи может быть 0,05%, но эффективная установка десульфации расплава перед кислородно-конвертерной выплавкой уменьшит ее содержание до 0,01%. Наиболее распространенные обессеривающее реагенты, известь, карбид кальция и магния — используется отдельно или в комбинации — вводят в горячий металл через кислородные фурмы. Серосодержащих соединений представляют шлак, однако, если бы только богатый для серы шлак был обезжирен перед тем, как жидкий чугун льется в конвертер, фактически содержание серы будет выше уровня ожидания при пробе металлического анализа.
Заключение
Плавка в конвертерных сооружениях считается морально устаревшей техникой, но ее продолжают использовать по причинам оптимального сочетания производительности и финансовых затрат на обеспечение процесса. В немалой степени востребованности технологии способствуют и конструкционные достоинства применяемого оборудования. Та же возможность прямой загрузки лома металла, шихты, шлама и других отходов, хоть и в ограниченном объеме, расширяет возможности для модификации сплава. Другое дело, что для полноценной эксплуатации крупногабаритных конвертеров с возможностями поворота требуется организация соответствующего помещения на предприятии. Поэтому осуществляют выплавку с кислородной продувкой в больших объемах преимущественно крупные компании.